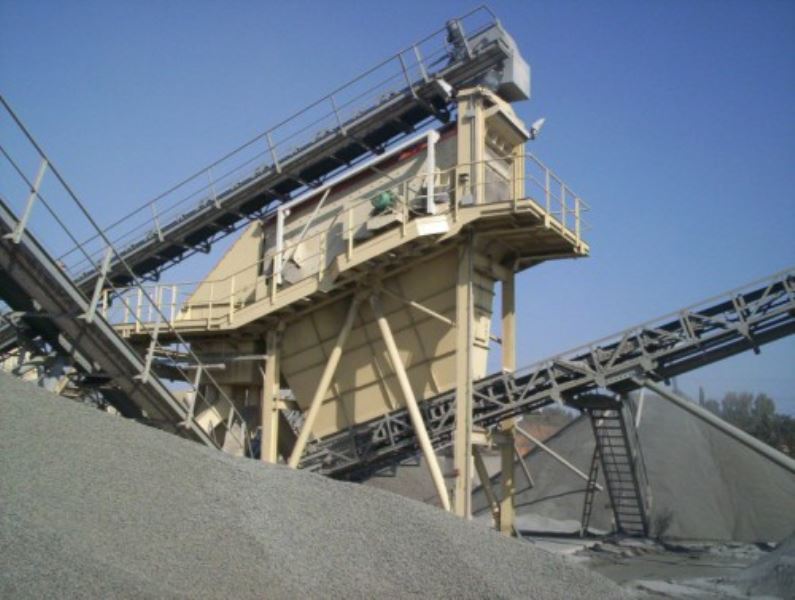
Impianti di Frantumazione: Come funzionano e quanto possono costare
Gli impianti di frantumazione rappresentano una soluzione industriale fondamentale per ridurre il volume di materiali come rocce, minerali e altri solidi. Questi impianti sono ampiamente utilizzati nel settore minerario, nell'edilizia e nell'industria della produzione di inerti. Grazie alle moderne tecnologie, oggi è possibile ottenere processi di frantumazione più efficienti, con una maggiore ottimizzazione dei consumi e un impatto ambientale ridotto. In questo articolo analizzeremo il funzionamento di un impianto di frantumazione, i principali componenti e i costi da considerare.
Struttura di un Impianto di Frantumazione
Un impianto di frantumazione è composto da diverse sezioni operative che garantiscono un processo efficiente e continuo. Le principali componenti includono:
- Ricezione e distribuzione del materiale da frantumare, che può avvenire tramite caricatori, nastri trasportatori o tramogge di alimentazione.
- Stoccaggio e gestione del prodotto della frantumazione primaria, per garantire una distribuzione uniforme del materiale nei successivi stadi di lavorazione.
- Uno o due stadi di frantumazione secondaria, con frantoi a cono o a urto per ottenere una riduzione ulteriore del materiale.
- Circuito chiuso o aperto con un vaglio, in base alle esigenze di selezione granulometrica.
- Stoccaggio del prodotto finale, organizzato in cumuli separati in base alla granulometria del materiale ottenuto.
- Sistemi di trasporto, come nastri o elevatori, per spostare il materiale tra le varie fasi del processo.
- Sistemi di controllo, pesatura e campionamento, per garantire la qualità del materiale prodotto.
Schema Tipico di Frantumazione
Il materiale grezzo viene introdotto nella tramoggia di alimentazione (1), da cui può seguire due percorsi:
- Entrare direttamente in un mulino a martelli (2) per una riduzione primaria del volume, spesso utilizzato per materiali di media durezza.
- Essere indirizzato direttamente a un vaglio a due piani (3) per una prima selezione dimensionale, particolarmente utile per materiali già parzialmente ridotti.
Dopo il passaggio nel mulino, il materiale frantumato esce (4) ed entra nel vaglio per una separazione granulometrica. I materiali di dimensioni maggiori vengono ricircolati al mulino per una nuova lavorazione (6), creando un circuito chiuso. Il materiale che supera il vaglio viene successivamente inviato a un vaglio a quattro piani (8), formando un circuito aperto, che consente di separare in modo più efficace le diverse granulometrie.
Alla fine del processo, il materiale viene suddiviso in quattro diverse granulometrie, ognuna delle quali forma il proprio accumulo, pronto per essere utilizzato nelle successive fasi produttive o commercializzato.
Costi di un Impianto di Frantumazione
Il costo complessivo di un impianto di frantumazione dipende da diversi fattori, tra cui la capacità produttiva, la qualità dei materiali utilizzati e i costi di gestione operativa.
1. Manodopera
La gestione dell’impianto richiede solitamente un operatore per la sorveglianza e la conduzione, mentre in situazioni più complesse potrebbe essere necessario un secondo addetto per facilitare la distribuzione del materiale. Questo è uno dei costi più rilevanti da considerare, in quanto dipende anche dalla necessità di turni di lavoro continui per garantire una produzione costante.
2. Consumo di Energia
L’energia necessaria per il funzionamento dell’impianto varia in base alla capacità installata. In genere, il consumo energetico per la frantumazione di un materiale oscilla tra 2.2 e 3.5 kWh per tonnellata, ma in alcuni impianti di ultima generazione con sistemi di recupero energetico è possibile ridurre i consumi del 10-15%.
3. Usura dei Componenti
L’usura è fortemente influenzata dalla durezza e dall’abrasività del materiale trattato. In molti casi, il costo dell’usura del metallo è direttamente proporzionale al consumo energetico, rappresentando una voce di spesa significativa. È fondamentale scegliere materiali resistenti per i componenti soggetti a maggiore sollecitazione, come i martelli del mulino e le piastre dei frantoi.
4. Forniture e Manutenzioni
- Le forniture (lubrificanti, materiali di ricambio, utensili di manutenzione) hanno costi paragonabili a quelli dell’energia impiegata per il processo.
- La manutenzione preventiva è essenziale per garantire il corretto funzionamento dell’impianto e prevenire guasti improvvisi che potrebbero interrompere la produzione, riducendo la produttività e aumentando i costi di riparazione.
- Alcuni impianti più avanzati utilizzano sistemi di monitoraggio remoto, che permettono di prevenire guasti e migliorare l’efficienza operativa.
5. Ammortamenti e Investimenti
L’ammortamento delle attrezzature varia in base al tipo di materiale trattato e alla tipologia di impianto. Solitamente, un impianto di frantumazione ha un ciclo di ammortamento compreso tra 5 e 10 anni, ma grazie a nuove tecnologie e a impianti modulari, oggi è possibile ridurre i costi iniziali suddividendo l’investimento in fasi successive.
Gli impianti di frantumazione fissi e gli impianti di frantumazione mobili sono essenziali per molte industrie e il loro costo complessivo dipende da numerosi fattori, tra cui la manodopera, il consumo energetico, l’usura dei componenti e le spese di manutenzione. Una progettazione attenta e un'ottimizzazione dei processi possono contribuire a migliorare l’efficienza e ridurre i costi operativi, garantendo un impianto performante e durevole nel tempo. Inoltre, grazie alle recenti innovazioni nel settore, è possibile migliorare la sostenibilità degli impianti, adottando soluzioni più efficienti e meno impattanti dal punto di vista ambientale. Investire in tecnologie avanzate per la frantumazione consente non solo di ridurre i costi operativi ma anche di migliorare la qualità del prodotto finale e la competitività sul mercato.